فهرست مطالب
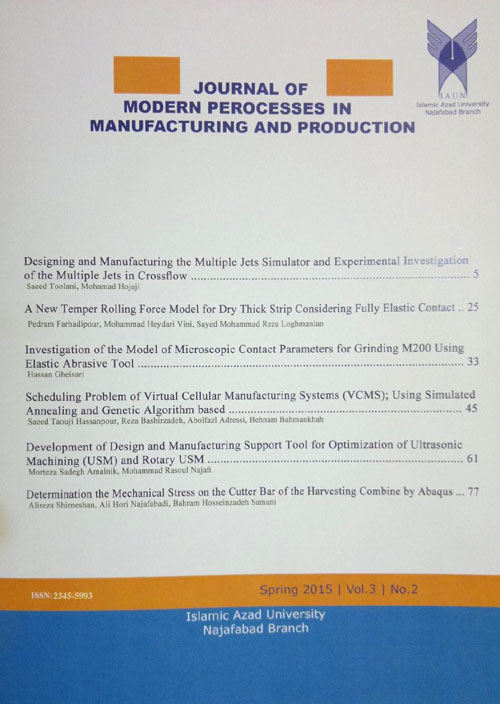
Journal of Modern Processes in Manufacturing and Production
Volume:9 Issue: 3, Summer 2020
- تاریخ انتشار: 1399/07/20
- تعداد عناوین: 6
-
-
Pages 5-12
The high strength carbon steels such as API X65 is widely used to build the pipelines. In this study, the corrosion behavior welds region of the gas pipeline was studied. For this purpose, Shield Metal Arc Welding (SMAW) was used to evaluate the proposed method. The welding processes were performed with E6010, E6013, and ER70S-6 electrodes as filler metal and welding carried out in 3 passes by a single butt welded method. The corrosion behavior was determined in the gas fluid solution at environment temperature using potentiodynamic polarization test. The microstructure of the base metal, weld zone, and heat-affected zone were investigated with optical microscopy. Results show that the microstructure changes that formed during the welding process were correlated with electrochemical results. And the corrosion performance of the weld joints was influenced by the type of filler metal. As the welded sample with ER70S-6 has high corrosion resistance in comparison to other electrodes.
Keywords: Bone Scaffold, Implant, Additive Manufacturing, numerical analysis -
Pages 13-22Computer analysis of image objects starts with finding them-deciding which pixels belong to each object. Digital elevation maps or models (DEMs) are arrays of numbers representing the spatial distribution of terrain elevations. They can be seen as gray-scale images, whereby the value of a pixel represents an elevation rather than a luminance intensity (the brighter the gray-tone level of a pixel, the higher the elevation of the terrain point corresponding to this pixel). Useful applications of DEMs can be found in civil/rural engineering, geographic information systems (GIS), geomorphology, water resources management, photogrammetry, satellite imaging. A watershed is defined as a region of land that assists in draining water (usually rainwater) into a river or a creek. It is an area of high ground through which water flows into the river or creek. Simply defined, the watershed is a transformation in grayscale images. This technique aims to segment the image, typically when two regions-of-interest are close to each other, their edges touch. Thus far, we have discussed segmentation based on three principal concepts.Keywords: image processing, Maps Production, Watershed Algorithm, Computer-integrated Manufacturing Systems
-
Pages 23-39
Material removal rate (MRR) and cutting volume efficiency (αVol) in laser cutting of commercial polyamide (Nylon) sheets have been studied in this research. A CO2 laser cutting machine with the power of 100 W was used to cut polyamide (PA) sheets with thicknesses of 2 to 8 mm. The beam spot size on the upper surface of the sheet was 0.1 mm. The maximum cutting speeds for a variety of powers and thicknesses were specified under the same other laser cutting parameters. The specific point energy (Esp) was calculated for every combination of maximum cutting speed and power. Results show that for a given power, the maximum cutting speed exponentially decreases with increasing sheet thickness. The MRR increases logarithmically with power and for a given power, it rises as the sheet thickness decreases. The αVol increases with power until it reaches the apex of efficiency, then it slightly reduces with increasing power. Overall, the αVol decreases with increasing sheet thickness and Esp.
Keywords: CO2 Laser Cutting, Polyamide (PA), material removal rate, kerf width -
Pages 41-50One of the most important methods to reduce metal corrosion and improve erosion resistance is to use strip cladding with electro slag welding. Applying the strip electrode (E316l), cladding performed on the layer of steel (5A-516) with this process. With changes in the thickness of cladding layers and the number of these layers, the percentages of ferrite and carbon in samples obtained by WRC equipment were analyzed. The optical microscopy is used to investigate the microstructure of different cladding layers in this research work. Hence, with the increase in the percentage of carbon, the sensitivity of stainless steel to grain boundary corrosion increases. With the reduction of ferrite percentage, the sensitivity to hot cracking increased too, so the overall results indicate that with an increase in the thickness of the first cladding layer, the amount of carbon in this layer increases, this phenomenon reduces the percentage of ferrite in it. Hence, by increasing the number of cladding layers, the amount of carbon percentage reduces considerably while the ferrite percentage reaches the desired amount.Keywords: Cladding, Electro Slag Welding, stainless steel, Carbon Ferrite Percentage, Strip Electrode
-
Pages 51-63The science of maintenance and the active life of the equipment is becoming increasingly important and is defined as a subset of asset management. This necessitates the design and development of a maintenance planning model for the supply chain. This research in the production and distribution program of the spare parts supply chain system, according to the specific and definite order and demand program of users in periods, leads to cost reduction and achieving economic goals in the production unit. In order to achieve this goal, some limitations for model equilibrium and justifying the answers obtained from the model solution are presented, in which we have achieved the optimal answer using the genetic algorithm method in MATLAB software. The present study is descriptive in terms of method and nature and applied in terms of purpose. This research has been done in terms of cross-sectional time and in six time periods and has no specific period. Data were collected through interviews and information available in the production unit of Rahyab Sanat Sepahan Company. According to the functions, the goal of minimizing system costs includes minimizing production, storage, and distribution costs, as well as reducing the difference between actual production time and nominal production capacity in the target function has been investigated. Reality can help make acceptable decisions despite various fluctuations in production lines, distribution centers, and transportation costs.Keywords: Probability Density Function, Spare Parts, Supply chain design, Maintenance-Repair-Operation
-
Pages 65-72Joining two dissimilar metals, specifically Mg and Al alloys, using conventional welding techniques is extraordinarily challenging. Even when these alloys can be joined, the weld is littered with defects such as cracks, cavities, and wormholes. The focus of this study was to use friction stir welding to create a defect-free joint between Al 2139 and Mg WE43. The design included an 11 mm scrolled and concave shoulder in addition to a 6 mm length pin comprised of two tapering, threaded re-entrant flutes that promoted and amplified material flow. Upon completion of this project, an improved experimental setup process was created as well as successful welds between the two alloys. These successful joints, albeit containing defects, lead to the conclusion that the tool used in the project was ill-fit to join the Al and Mg alloy plates. As a result of this aggressive pin design, there was a lack of heat generation towards the bottom of the pin even at higher (800-1000 rpm) rotation speeds. This lack of heat generation prohibited the material from reaching plastic deformation thus preventing the needed material flow to form the defect-free joint.Keywords: Friction Stir Welding, Al alloy, Rotation speed, Mg alloy